|
|
|
|
|
|
|
 |
Broach Sharpening Machines |
|
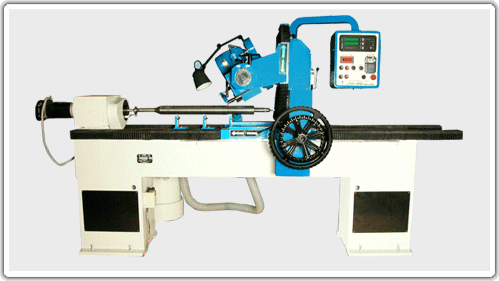 |
|
Manufactured as per International ‘Non-CNC
Design’ for better life at low cost.
This machine is most suitable to meet the general requirements of sharpening
broaches in small or large industries. This low-cost machine is designed
specifically for resharpening as well as nicking operations of circular and
flat broaches, back off operation on cutting teeth of flat broaches. Its
rigid bed, well balanced and vibration-free grinding spindle enable the
machine to perform with high precision.
MACHINE BED Two sizes:
(a) Standard for broaches upto 2000 mm length
(b) Extended for broaches upto 2300 mm length.
Stress-relieved, fine grain casting machine bed provides sufficient
rigidity, damping of vibration and stability against distortion. The guides
of the bed are protected by specially designed bellows.
Grinding Spindle is accurately balanced with specially designed high
precision matched pair bearings. Required speed can be obtained by rotating
speed changing knob having 5 steps.
The carrier facilitates swivel of the grinding spindle upto 900 around
horizontal axis. With this facility the grinding spindle can be set to the
required angle to get proper rake angle. This also makes it possible to back
off tooth top on the flat broaches with swivel of the grinding spindle
carrier slide.
Integral headstock casting increases rigidity keeping the machine
vibration-free. Required speed can be achieved by rotating speed changing
knob. The speed obtained will be displayed on Digital Speed Indicator.
Spring loaded tailstock quill with 25 mm stroke helps in quick withdrawal of
the sleeve and setting of the broach between centres with the correct spring
pressure.
Rack and pinion arrangement with gear train provides smooth and effortless
movement of the saddle along the bed length and slide carrier in vertical
traverse. Separate control wheels are provided to operate the saddle and the
spindle carrier.
Manually operated lubrication pump facilitates oiling of all moving parts.
FREQUENCY CONTROLLED AC DRIVE FOR GRINDING SPINDLE enables
selection of the suitable spindle speed.
DUST EXTRACTION SYSTEM is ‘suction system’ mounted behind
the machine and driven independently. Powerful suction extracts grinding
dust promptly, ensuring safety and cleanliness.
NICK GRINDING ATTACHMENT for nicking operation (providing
chip breakers) on cutting teeth of circular as well as flat broaches.
DIGITAL READ OUT (DRO) UNIT For accurate positioning of the
saddle and the grinding spindle while sharpening.
|
|
Key Parameters:
|
Must for all Broach users for in-house
sharpening for better life, accuracy & no down time.
Low cost high performance machine.
For resharpening Broaches with unique Nick Grinding and back off
attachments. Digital Read Out to control sharpening & accuracy.
Rigid construction, Well balanced, vibration-free grinding spindles.
Sharpening Range:Max. broach dia. 120mm, Max. width of flat
broach 200 mm, Max. distance between centres 2000/2300 mm, Max. sharpening
length 1500/1800 mm.
|
|
|
|
|
|
|
|
|
|
|
|
|